To the place where "good design" was created
Good design, excellent design, design that opens up the future, ideas that move people's hearts, and actions that lead society always have small beginnings.
Interviews with designers at the birthplaces of good design to find hints for the next design.
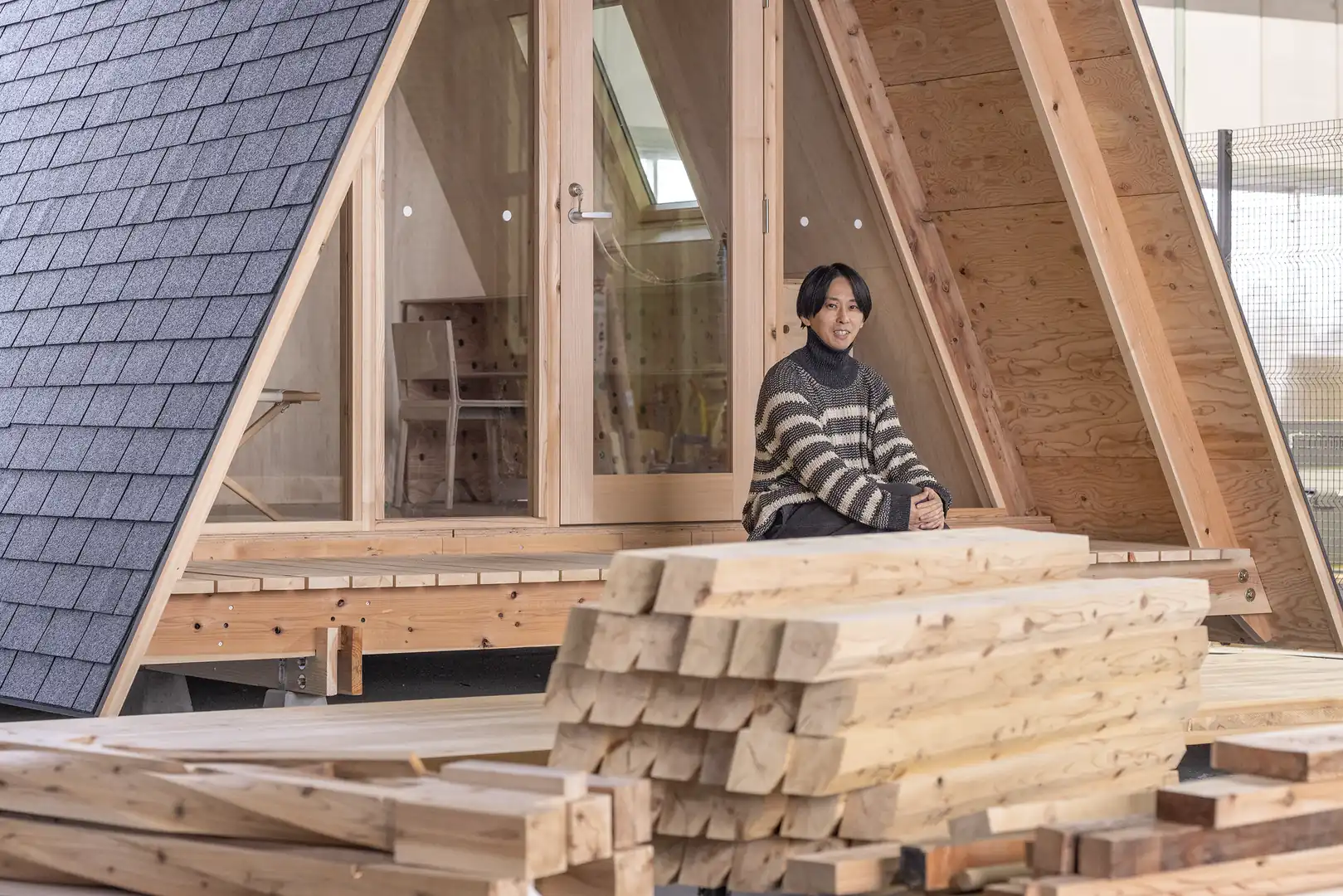
Destination
VUILD, inc.
Transforming the World of Architecture through Digital Fabrication (Part 1)
2025.02.21
Digital fabrication is attracting attention for accelerating the pace of manufacturing. The Ministry of Internal Affairs and Communications defines digital fabrication as technology which produces creations based on digital data. There are many devices including 3D printers, 3D scanners, CNC milling machines, robotic arms, and sensors, and their expansion within the field of architecture is particularly impressive. The VUILD architectural group is producing cutting-edge examples of this.
House for Marebito, an accommodation facility that was selected for the GOOD DESIGN GOLD AWARD in 2020, was an ambitious work created by meticulously cutting local wood with a digital milling machine and assembling the pieces like a plastic model kit. The company’s founder, Koki Akiyoshi, is pursuing the democratization of architecture and continues to boldly implement this principle in order to bring about a society in which anyone can become a maker. What he has in his sights is changing the Japanese construction industry. It was also an activity to propagate innovation.
Making architecture like a product
– VUILD’s activities have the potential to change the architecture of the future. Today, I would like to ask you about your wide-ranging activities and how these differ from ordinary architectural design.
Koki Akiyoshi (President and CEO, VUILD) VUILD was established in 2017 as an architectural design start-up company aiming to bring about a society in which anyone can become a maker. At the heart of its activities was ShopBot, a digital milling machine manufactured by the American company ShopBot Tools, Inc.
This is equipped with software for 2D and 3D cutting, and is a machine using which anyone can quickly give shape to their ideas through simple operations. Although it has high-level capabilities, it is relatively affordable, and in the U.S., where DIY is very popular, individuals own them, placing them in their garages and using them for their hobbies. They make things like baseball scoreboards and stage sets for plays.
Akiyoshi We have started a business to import and sell these products and have introduced them to hilly and mountainous areas rich in forest resources. At the same time, we are building an autonomous decentralized network where anyone can make furniture and buildings as long as they have the data.
This is because we want to bring about a world where anyone, anywhere, can make the furniture and buildings necessary for their lives by themselves, using materials from their own area.
– House for Marebito, which won a GOOD DESIGN GOLD AWARD in 2020, was designed as a case study. It was evaluated by the judges at that time as making architecture like a product and a new activity enhancing the mobility of architecture.
Akiyoshi House for Marebito was designed as a lodging facility for people (bito) who visit once in a while (mare) in a mountainous village in Toyama Prefecture with a population of about 600 people. In Japan, the population of marginal settlements in hilly and mountainous areas continues to decline, and they are desperate to attract people to come and live there. However, this is not going as well as they had hoped.
With the COVID-19 pandemic, work was carried out remotely in various places, and we wondered if there was a way for people to own residences which were somewhere between homes and accommodation. Therefore, we came up with the idea of shares held jointly by investors who supported us through crowdfunding and Hideo and Akemi Ueda, residents of the village.
Akiyoshi In marginal settlements, resources are not used effectively. What is more, they are treated as though they are a dime a dozen. This area is home to the village of Gokayama, a World Heritage Site of gassho-style, a traditional technique houses with steep thatched roofs. So we tried to reinterpret and update these traditional gassho-style houses in a modern way. By designing a building that can be constructed from small and light parts, many people can participate in the project, and the skeleton (framework) can be completed in a day.
– In other words, you conceived of this project as a digital fabrication case study, and it got off the ground as you involved the local community and citizens, right? The machinery for processing was installed in a nearby sawmill, which stimulates local economic circulation, avoids transportation costs, and reduces the environmental impact.
Transformation due to a positive proposal, rather than to solve problems
– After graduating from School of Architecture of Shibaura Institute of Technology, you joined Keio University’s Graduate School of Media and Governance. Did you learn about digital fabrication while you were at graduate school?
Akiyoshi I belonged to a research team developing 3D printers. At the time, I was at an international conference for people who used digital manufacturing machines, and the world’s discussion was focused on how to localize.
The argument was that even if the same machines were introduced throughout the whole world, their output should not move toward homogenization, but rather confront regional and inherent characteristics. There was a clear intention not to follow the same path as modernism and globalism.
Akiyoshi From there, attention began to be paid to materials for each region, such as whether these could be produced by solidifying desert sand using sunlight, or by injecting soil. Two-thirds of Japan’s land area is forested. When wood is used in the U.K., for example, it is often imported from Austria and processed in Belgium or somewhere similar; wood is not something found close at hand.
At that time, the participants said to me, “It’s nice that you can readily get so many kinds of trees, such as cherry trees, in Japan.” I realized once again that Japanese forest resources had advantages as local materials.
– Timber and wooden buildings have attracted global attention in recent years. On the other hand, the price of the trees in Japan’s mountain areas is not constant, and the process of felling, sawing, processing, and transportation is opaque in some areas. The reality is that these factors prevent resources from being fully utilized. Were there any barriers to entry as a newcomer?
Akiyoshi I didn’t get involved due to any idea of solving such problems. I visited local woodworking shops and sawmills to introduce these machines and ask if they were interested. When I did so, replies like “Could we do something like this with the materials we have here?” gave me a sense of the possibilities. Sensing an enthusiastic response to the idea of making things was the start of it.
The reason these people are interested in processing is that selling wood solely as a material is becoming unviable as a business. It is because they want to increase their profit margin through adding value by processing and selling wood as products like furniture. Normally, you would have to pay for shipping to a processing facility outside your area, but with digital fabrication, you can make whatever you want on the spot. I guess I got one request after another because they could turn this into a business with good cost performance.
– I see. If you attempt to get involved with local issues, there is opposition; but by approaching people with a positive attitude, saying “We can do this,” they supported the idea and the number of users grew. Isn’t that right? If wood starts to be used efficiently across a wide area, it will also promote the revitalization of forests.
Akiyoshi There are currently over 250 ShopBots in operation in Japan. If what we are doing prompts the revitalization of timber-growing areas, we may eventually be able to solve the problems faced by forestry.
If new machinery comes into these areas, young people will get jobs there and start using the machinery. Forestry and timber-related jobs have long faced a shortage of staff, but as these occupations become more attractive, young people may enter the industry. I believe it is an effective driver for revitalizing local industry. In fact, the number of interesting people working in this field has increased over the past few years.
Create leeway for the ownership of architecture
– Local people participated in the construction of House for Marebito and Shodoshima The GATE LOUNGE. This not only reduces costs and improves efficiency, but is also a valuable opportunity for them to experience architecture.
Akiyoshi Working together with the villagers and other people involved means building a connection with civil society: participating in building projects using local timber, connecting with nature, and connecting with the local community. Our strength is in facilitating these connections.
Akiyoshi We place importance on having people take ownership of architecture. Even if the developer pays the construction costs, it is the town’s residents or the local people who actually use the building. If we can create leeway for people to get involved with the building process, they will also become involved with it as their own building after it is completed. I think that the fact that this system grows up naturally is important to the project.
A platform to eliminate dependence on people
– Milling machines using numerical control (NC) technology, known as NC router machines, have already been in use in Japanese factories. However, only craftsmen could master them. ShopBot can be used by anyone, and that’s what makes it different from conventional products.
Akiyoshi Equipped with computer control, this is a more advanced milling machine, a CNC router machine, yet it is easy to handle and so there is a much lower barrier to using it. We also provide training on how to use the machine when it is introduced, because we are the people who are most familiar with it.
The thought behind its design is fundamentally different from those for previous designs. The machine itself is delivered as separate parts, so we work with the customer from assembly to wiring. That’s why, even if there is some kind of trouble or it breaks down, you can fix it yourself.
– Typically, highly specialized machines are managed by the seller, so they end up as black boxes.
Akiyoshi I wanted to put the know-how related to this machine out in the open, so that anyone could use it. But even though the machines are designed to be used by anyone, you still have to gain experience to become an operator. And so, even if someone learns a skill, you won’t be able to run the machine if that person quits. In that case, we wanted to create a system that did not depend on people.
So we developed EMARF, a platform that seamlessly connects design and fabrication. We came up with this name by turning the word “frame (the existing framework)” backwards, to reflect the concept of turning manufacturing systems and processes around, and transforming them into more open and accessible forms.
EMARF does not require a craftsman’s knack for creating data. All you have to do is input the design data saying how you want to cut the timber, and it can automatically generate a machine code that rearranges the materials and operates the machine. This truly makes it possible for anyone to make things.
– You developed not only the machine, a hardware, but also the software to run it, didn’t you?
Akiyoshi Almost all the machines are located in mountain villages. On the other hand, the people who want to make things, like designers, are in town. We thought that the only way to connect them was via the Internet, so we simultaneously created a platform to place and receive orders on our website.
You can access the information about how much it will cost to mill this material in that region, anywhere in the country. Accessing EMARF gives you the ability to manufacture without having to buy machinery.
– You can say that this is the democratization of architecture and manufacturing, right?
Akiyoshi The construction industry as a whole is currently facing a shortage of human resources. The number of carpenters, which was 800,000 in the 1980s, is predicted to fall below 200,000 by 2030. In the sense that people who can make things are disappearing, this implies that people who can make more challenging and complex designs will also disappear. But if you use EMARF for production in the factory, you can shorten the processing time on site, so you can shorten the construction time and tackle complicated things.
Highly expressive designs also tend to be high-expenditure, but EMARF can be used to secure parts while considering the cost, reduce the number of man-hours required to construct the site, and adjust the project. In fact, design firms which are part of larger organizations and projects by major construction companies are already running on the EMARF platform.
Generating a wave through a chain of creativity
– Digital fabrication has its roots in parametric design, which uses algorithmic parameters to create 3D models. Some well-known examples are the Guggenheim Museum Bilbao, designed by Frank Gehry, which made use of CAD and CNC technology to create complex curved surfaces, and the work of those such as Zaha Hadid Architects and Foster + Partners.
With this design method, architecture and cities attained freedom of form. Will digital fabrication accelerate freedom of design in the same way?
Akiyoshi Yes. If you want to create free forms, we will provide the ways needed to make them, so that they can probably be made to come in within budget.
– In February 2024, you won the Japan Architecture Award – Architecture Awards for Everyone –, for the Learning Architecture for Learners (HIVE building) which you designed and built on the campus of Tokyo Gakugei University. I hear that this is a facility open to students, faculty, and the community, and was intentionally left unfinished.
Akiyoshi We designed this building as an open-ended place where users can enlarge themselves, aiming for an experimental entity that could also be used as a teaching tool. It is a digital fabrication workshop which implements an innovative educational program.
House for Marebito was a building of 50 square meters, on the level of a cabin, but this facility in Tokyo Gakugei University has been expanded to a scale of 300 square meters. We are taking on the challenge of making concrete formwork here. The reason is that if concrete formworks can be freely designed, concrete can then be freely made at low cost.
Akiyoshi This is a reinforced concrete structure using cross-laminated timber (CLT) as formwork, and all the CLT panels were processed at VUILD’s own factory. The cost of using concrete is cut by 60% compared to the conventional concrete shell method, allowing us to reduce the cost to 60%.
– The examples of architecture built by VUILD hint at the potential of digital fabrication, don’t they?
Akiyoshi VUILD is not simply a platform: by using the platform to create our own examples, we provide inspiration to those who want to use the platform. The creativity ripples out to other people, and the people who are influenced by it ask us if they could do the same thing. In our activities, we are conscious of setting these cogs in motion.
– Ancient people built their huts themselves. Your activities remind me of that. This could turn into a breakthrough in returning architecture into people’s hands, or in breaking down the old conventions and closed nature that persist in the architectural industry and changing the ways we interact with architecture. In spite of its enormous transformative potential, VUILD is flexible as an actor.
Akiyoshi I compare the company to a tree, and I sense the branches and leaves growing now. Let’s say that we are continually branching and spreading out.
The ideas that anyone can make things and that things can be made in the community are the roots of this tree, and the more ShopBot machines are sold, the more users there will be, and the roots will grow. Our own examples increase, serving as branches and leaves, and once a template is in place, the branches and leaves will continue to divide and grow. There are also projects in which we participate as design support for other designers’ designs. We are developing our activities with the precise intention of generating a wave through a chain of creation.
– By doing so, you can respond to current social issues.
Akiyoshi A stance of not over-focusing on the domain is important. I believe that the more we grow our branches and leaves and develop points of contact, the more we will be able to respond to the diverse needs and circumstances in the world.
As in the case of Tokyo Gakugei University, the amount of concrete used and carbon (carbon dioxide) emissions can be dramatically reduced by changing the ways in which things are made. It is not impossible to tackle larger buildings, such as skyscrapers, with the same gaze.
Tall buildings are a bundle of carbon emissions, so we can cut a massive amount. The perspectives and strengths that were put into practice in small projects will be introduced to large projects, transforming them. I think that this is the biggest mission assigned to me as an architect.
– Thank you very much. In Part 2, Akiyoshi tells us about how he wants to change the future of architecture, including his recent projects.
In GOOD DESIGN TANBOU (=exploring), we deliver interviews and introduce works based on a certain subject. This time, the theme is “creation wave.” When we unravel “Good Design,” we can see how one “Good” perspective or action leads to another “Good” one, which embodies good things in waves. We cover the story of how new ideas are connected to each other to create good things and events.
House for Marebito
VUILD, inc.
It is a joint ownership-type accommodation facility funded through crowdfunding, and built with the introduction of digital fabrication technology. Making use of local timber in a village with a population of about 600, the project proposes a lifestyle in which people move continuously back and forth to mountain villages in a way which feels more than tourism but less than migration. By completing the entire process from timber procurement to processing and construction within a 10 km radius, the project is tackling the problems of forestry decline and marginalization of settlements.
- Award details
- Award details 2020 GOOD DESIGN GOLD AWARD https://www.g-mark.org/en/gallery/winners/9e34f37b-803d-11ed-af7e-0242ac130002
- Designer
- Koki Akiyoshi, Hayato Kurobe, Kazuya Takano, Koki Ogawa, Hanako Kato, VUILD, Inc. (Design) + yasuhirokaneda STRUCTURE Yasuhiro Kaneda (Structure) + DE. Lab (Facility)
Tomoko Ishiguro
Editor/writer
After working in the editorial department of “AXIS,” she became a freelancer. She writes, edits, and plans, with a focus on design and life culture. Her major editorial works include LIXIL BOOKLET series (book, LIXIL Publishing) and “Oishisa no Kagaku” (magazine, NTS Publishing).
Kenji Masunaga
photographer
After working at Roppongi Studio and Nacasa & Partners, he established masphoto in 2013. With a focus on subjects such as architecture, interior design, and landscape, he is active across various genres such as magazines and advertising in general.